Accelerometers
An accelerometer or vibration sensor or shock measurement sensor is an electromechanical device that will measure acceleration forces. These forces may be static, like the constant force of gravity pulling at your feet, or they could be dynamic - caused by moving or vibrating the accelerometer. Acceleration is the rate of change of the velocity of an object. They measure in meters per second squared (m/s2) or in G-forces (g). A single G-force for us here on planet Earth is equivalent to 9.8 m/s2, but this does vary slightly with elevation. Accelerometers are useful for sensing vibrations in systems or for orientation applications. There are two classes of accelerometers in general: AC-response and DC-response.
In an AC-response accelerometer, as the name implies, the output is ac coupled. An AC coupled device cannot be used to measure static acceleration such as gravity and constant centrifugal acceleration, for example. It is only suitable for measuring dynamic events. A DC-response accelerometer, on the other hand, is dc coupled, and can respond down to zero Hertz. It therefore can be used to measure static, as well as dynamic acceleration.
The most common AC-response accelerometers use piezoelectric elements for their sensing mechanism. Under acceleration, the seismic mass of the accelerometer causes the piezoelectric element to “displace” a charge, producing an electrical output proportional; to acceleration. Electrically, the piezoelectric elements look like a source capacitor with a finite internal resistance, typically in the order of 109 ohms. This forms the RC time constant which defines the high-pass characteristics of the device. For this reason, piezoelectric accelerometer cannot be used to measure static events. Piezoelectric elements can be natural or man-made. They come with varying degrees of transduction efficiency and linearity characteristics. Two types of piezoelectric accelerometer are available on the market – charge output type and voltage output type.
Two popular sensing technologies are used in making DC-accelerometers: Capacitive and Piezoresistive.
Capacitive type (based on the capacitance changes in the seismic mass under acceleration) is the most common technology used for accelerometer today. They are made popular by large commercial applications such as air-bag and mobile devices. They employ Micro-Electro-Mechanical Systems (MEMS) fabrication technology which brings economy of scale to high volume applications, hence lower manufacturing cost. Due to its built-in amplifier/IC, its 3-wire (or 4- wire for differential output) electrical interface is straight forward, requiring only a stable DC voltage source for power.
Bandwidth of capacitive accelerometer is mostly limited to a few hundred Hertz’s (some designs offer up to 1500Hz) partly due to its physical geometry and its heavy gas damping. Capacitive sensor structure also favours the lower range of acceleration measurement. Maximum range is typically limited to less than 200g’s. Other than these restrictions, modern capacitive accelerometers, especially the instrument grade devices, offer good linearity and high output stability. Capacitive type accelerometers are most suitable for on-board monitoring applications where cost may be the driving factor. They are suited for measuring low frequency motion where the g level is also low, such as vibration measurements in civil engineering.
Piezoresistive is the other commonly used sensing technology for DC-response accelerometers. Instead of sensing the capacitance changes in the seismic mass (as in a capacitive device), a piezoresistive accelerometer produces resistance changes in the strain gages that are part of the accelerometer’s seismic system. The output of most piezoresistive designs is generally sensitive to temperature variation. It is therefore necessary to apply temperature compensation to its output internally or externally.
Bandwidth of piezoresistive accelerometers can reach upwards of 7,000 Hz. Many of the piezoresistive designs are either gas damped (MEMS types) or fluid damped (bonded strain gage type). Damping characteristics can be an important factor in choosing an accelerometer. In applications where the mechanical input may contain very high frequency input (or excite high frequency response), a damped accelerometer can prevent sensor ringing (resonance) and preserve or improve dynamic range. For very high g shock measurements, some piezoresistive designs can handle acceleration levels well above 10,000g’s. Due to its broader bandwidth capability, piezoresistive type accelerometers are most suitable for impulse/impact measurements where frequency range and g level are typically high. Piezoresistive accelerometers are commonly used in automotive safety testing, weapons testing, and higher shock range measurements beyond the usable range of VC accelerometers.
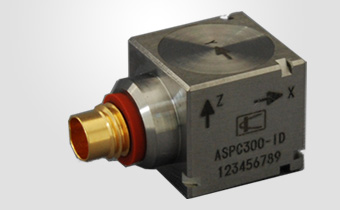
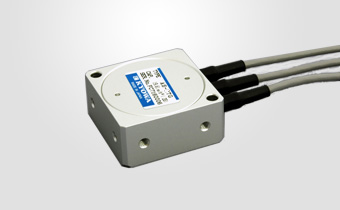
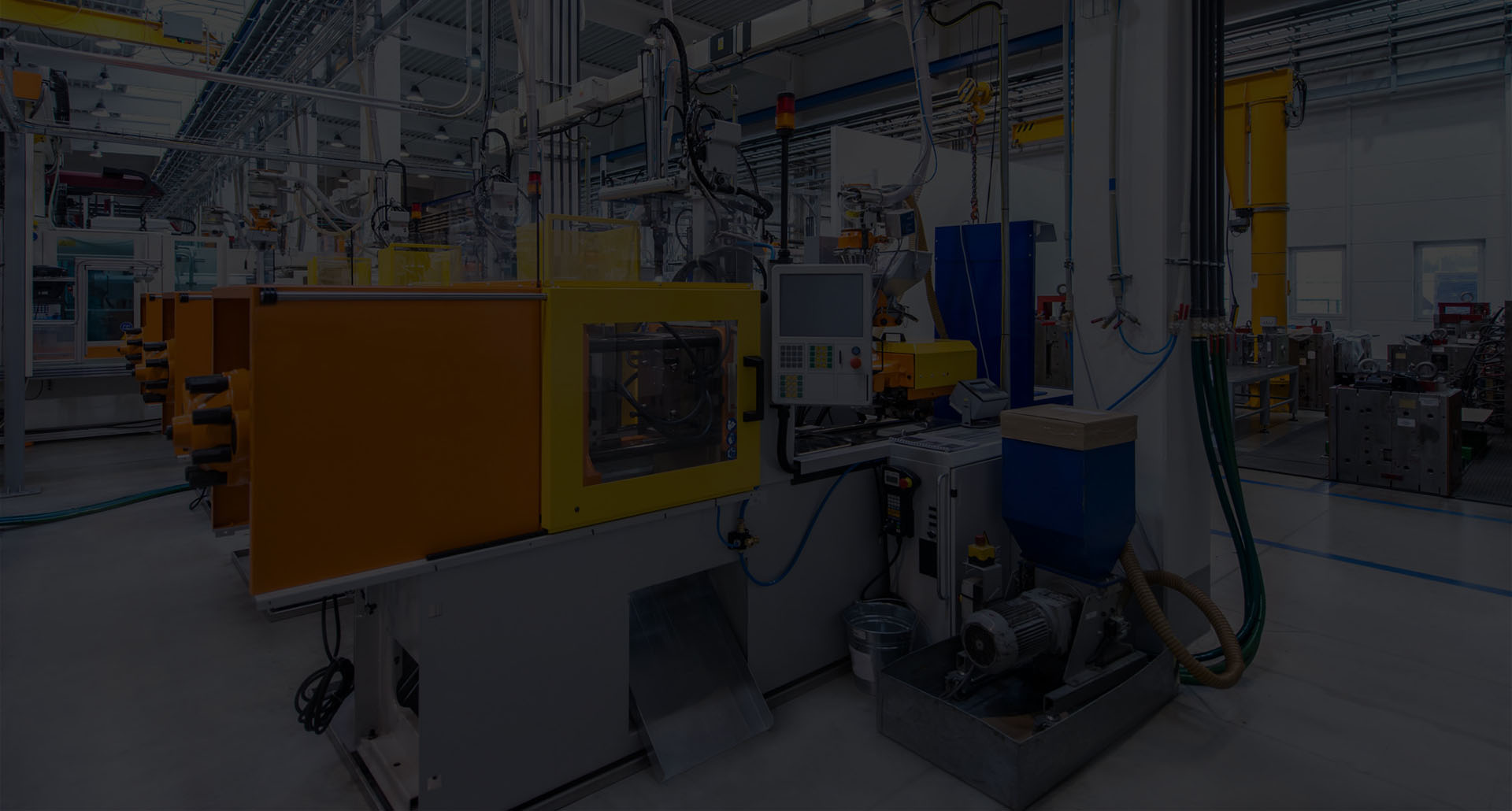
Intelligent Consulting Services, Seamless System Integration and Smart Turnkey Solutions for Modern Automation

Support for software-based creation of measurement projects.

Technical advice for mechanical sensor integration.
